A pugmill mixer, also known as a pug mill or paddle mixer, is a type of horizontal, continuous mixer used throughout a variety of industries to combine solid and liquid feed components into a homogeneous mixture.
Pugmill mixers are chosen for especially demanding settings in which the materials require a tough but thorough mixing action due to consistency, abrasivity, corrosiveness, or other material challenge.
Here’s a look at how these mixing devices work and why they’ve become so essential to operations requiring a rugged mixer.
Pugmill Mixer Construction and Industrial Uses
The pugmill mixer consists of a u-shaped trough in which two shafts fitted with pitched paddles counter rotate. The mixer has a cover and typically a spray system to incorporate liquid binders and additives.
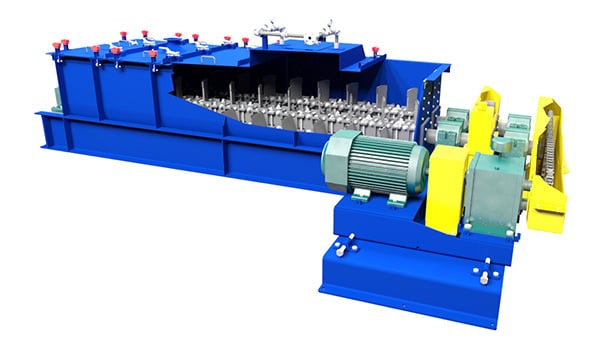
3D Rendering of a FEECO Pugmill Mixer with cutout to show interior
Spray system mounted on top of pugmill mixer; this particular mixer features a raised cover to improve the distribution of binder over the tumbling material bed.
The pugmill mixer is robustly built for long-term reliability and withstanding the rigors of demanding process environments. The mixer uses a medium shear, high-torque action ideal for combining abrasive materials and powering through heavy-duty loads. This has made it a key process component in blending copper concentrates, as well as processing steel mill byproducts for recovery.
In addition to mixing and conditioning materials, the pugmill mixer is also capable of producing rough agglomerates. Its ability to condition, agglomerate, and mix disparate components has also made it a favored approach to conditioning industrial wastes for landfill deposition.
In short, pugmill mixers have become the industry standard for heavy-duty applications requiring the homogeneous blending of solid and liquid feeds.
View of pugmill mixer trough exterior
Pugmill mixers also offer a high level of customization for tailoring a unit’s design to the specific needs of the application and material at hand. This might include the addition of access/inspection doors for viewing, doors for simplified cleanout, drains for wash down, venting systems for dust management, instrumentation, and more.
View from top, looking into the pugmill mixer. Spray system and inspection doors can be seen on the raised cover.
Pugmill Mixer Operation
The counter-rotating shafts, combined with the mixer’s high torque and medium shear, create a kneading and folding over motion inside the trough, which lifts material up through the center of the shafts, and pulls it back down the sides to create an intimate mixture of materials. This pulling action also helps to advance material through the mixer.
Counter-rotating shafts fitted with pitched paddles inside the pugmill mixer trough produce a kneading and folding motion
Agglomeration, or the actual formation of granules, is accomplished through 1) the addition of water or binder to the material while suspended, 2) the kneading motion that occurs between the paddles, and 3) the pulling action along the trough walls.
Agglomerates produced from conditioning in a pugmill mixer
Paddle arrangement can be modified to increase bed depth and retention time.
The pugmill mixer may be used as a stand-alone mixing and conditioning device, or as part of a larger agglomeration setup to create more refined granules. Typical retention time for a pugmill mixer is one minute, but could run up to five minutes, depending on the process goals.
A variety of practices in pugmill mixer operation should be followed for best results.
Pugmill mixer trough in fabrication
Pugmill Mixer Testing
It is not always clear whether a pugmill mixer will be the best fit for a given application. In these cases, pugmill mixer testing services can offer valuable insight into whether or not the machine will be a good fit. In the FEECO Innovation Center, for example, customers can test their material in a pugmill mixer for feasibility, as well as for gathering the process data necessary for scale-up and commercial unit design.
The pugmill mixer can be tested as a stand-alone device, or as part of a larger, continuous agglomeration setup involving drying and a recycle circuit as well.
Conclusion
Pugmill mixers are an excellent option for continuous industrial operations requiring mixing, conditioning, or agglomeration, particularly when the application requires a heavy-duty solution. Their ability to intimately mix solid and liquid feed components into a homogeneous mixture makes them an ideal fit for many applications.
FEECO is the leading manufacturer of custom pugmill mixers. In addition to manufacturing, we can also offer feasibility testing and process development services, as well as parts and service support. For more information on pugmill mixers, contact us today!