Pugmill mixers are a type of continuous horizontal mixer used for mixing, conditioning, and granulating bulk solid materials of nearly all types. These industrial mixers can be used as a stand-alone agglomeration device, or as part of a larger agglomeration setup.
However they are used, optimizing performance and equipment longevity are often central to the operation. Those looking to utilize the diverse capabilities of a pugmill mixer should consider the best practices provided here to get the most out of their pugmill mixer.
About Pugmill Mixers
Pugmill mixers consist of a u-shaped trough in which twin shafts fitted with pitched paddles counter rotate to thoroughly mix materials. The high-torque kneading and folding motion employed by the pugmill mixer is ideal for mixing moisture-laden or sticky materials, as well as those that are corrosive or consist of large lumps.
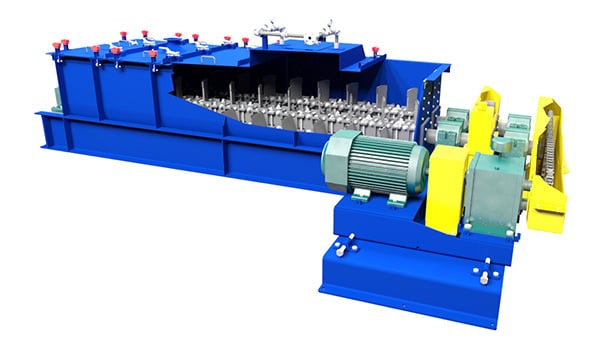
3D Model of a FEECO Pugmill Mixer (Pug Mill/Paddle Mixer)
Pugmill mixers can be found in a wide range of industries, accomplishing processing goals in an array of applications.
Best Practices for Pugmill Mixer Operations
The following recommendations provide a high-level guide for maximizing the return on investment when working with a pugmill mixer.
Use Multiple Binder Injection Ports
Pugmill mixers are best equipped with multiple injection ports. While it may not be necessary to utilize all of the ports at once, having multiple ports gives operators flexibility in responding to changes in production, or optimizing the spray distribution during start-up.
Operators should take advantage of these many ports, experimenting with different spray locations as needed to optimize the process, particularly in times of fluctuation.
For existing operations experiencing struggles in maintaining consistent production, retrofitting additional ports onto the unit may prove beneficial.
The FEECO Pugmill Mixer shown here is equipped with a raised cover and six spray ports.
Consider Alternative Materials of Construction
Pugmill mixers are typically constructed out of carbon steel. While this provides a suitable framework for many applications, other materials may be a better fit for operations with more specific requirements.
Stainless steel or other alloys may provide a better option for operations dealing with especially corrosive materials, those switching between different product runs, and more.
Choosing the appropriate material of construction contributes significantly to the life of the equipment, and in many cases, how smoothly the operation runs.
Explore Different Paddle Facings
Similarly, pugmill mixer operations should be open to trying different wear materials for lining the paddles.
Not surprisingly, the paddles wear the fastest in a pugmill processing operation and depending on the material being processed, may require routine replacement. For this reason, it is common practice to choose a facing material for the paddles that is most compatible with the material being processed so as to minimize wear.
Operations experiencing excessive or accelerated paddle wear should explore alternative facing options.
Maintain a Consistent Feed
A consistent feed is the basis for successful bulk solids processing in nearly any setting. Pugmill mixers are designed around a specific set of feedstock criteria, among them moisture content, chemical composition, and particle size distribution. When any one of these factors falls out of spec, processing will be affected and may require adjustment.
Similarly, the less variation that occurs in the feedstock, the more uniform the end product will be. A uniform feedstock also reduces the load on the operator, requiring fewer on-demand adjustments and reducing the potential for error to occur. As such, feed consistency should be a consideration in vendor selection when sourcing material.
Consider the Entire Process
Pugmills employed in a larger process should always be considered as such. Changes in production upstream of the pugmill mixer have the potential to impact mixer operation; problems appearing to originate in the pugmill mixer are often a result of changes that have taken place prior to the pugmill mixer.
Likewise, the pugmill mixer influences downstream processing, so problems that appear to originate at the end of the process could be the result of a change with the pugmill.
Because of this, any changes to equipment preceding the pugmill mixer should take into account how those changes will influence the pugmill mixer, and any changes made to the mixer itself must take into account how those changes will influence downstream production equipment. This must also be kept in mind during troubleshooting; each component contributes to the balance of the entire process.
Minimize Buildup
Buildup has the potential to cause a range of problems, from inconsistent product, to equipment damage, and an overall reduction in efficiency. Keeping buildup to a minimum is crucial to promoting equipment longevity and preventing premature wear on parts, particularly when it comes to processing abrasive materials.
Not addressing buildup will also foster accelerated corrosion when working with corrosive materials. Seasonal operations are especially likely to see damage to equipment if buildup is not cleaned out of the mixer prior to off-season.
Opt for a Site Audit
Site audits offer significant value in their potential to improve operational efficiency and equipment longevity. Depending on the goals of the inspection, audits may be in the form of an equipment audit, in which the mechanical integrity of the pugmill mixer is evaluated, or a process audit. Process audits typically address specific issues the operation is dealing with, but can also be used to generally improve process efficiency and product quality.
In addition to identifying issues and coming up with a plan of action for resolution, both types of audits also provide valuable benchmark data for future reference.
Utilize Automation
Outfitting the pugmill mixer with automation capabilities provides many benefits to the operation. By equipping the pugmill mixer with sensors incorporated into the PLC (programmable logic controller), various points of data can be collected, reported on, and even adjusted in real time from the operator interface.
Monitoring data such as current (amps), feed and product rates, torque, temperature, and more, gives the operator a complete picture of how the unit is performing and where potential problems may lie or adjustment might be needed. The PLC can also automatically adjust the amount of liquid being sprayed based on the amount of material entering the machine.
Consider Testing
All materials respond differently to processing in a pugmill mixer and the outcome can be hard to predict. Paired with the many variables in processing and any potential variation in feedstock, and achieving consistent output with the desired characteristics can be challenging. Those venturing into a novel process, or struggling with an existing one have a couple of options available to them.
First, they can seek out a rental pugmill mixer to conduct in-house testing on their material. Second, they can enlist the help of a testing facility such as the FEECO Innovation Center.
Feasibility testing in batch-scale equipment in facilities such as this helps confirm the process concept, while continuous pilot-scale testing reveals the process parameters necessary to reach the intended goals.
Conclusion
The diverse processing capabilities of the pugmill mixer serve a wide range of industrial applications. To achieve the most gains from this industrial mixer, operators should follow best practices such as using multiple spray ports, maintaining consistent feedstock, taking advantage of testing facilities, and more.
Backed by unmatched expertise, FEECO provides the industry’s most reputable pugmill mixers. All mixers are engineered around the specific process and material goals of the intended production line for optimal production and seamless integration. FEECO also offers comprehensive testing programs, rental equipment, and parts and service support for supporting pugmill mixer operations throughout their life cycle. For more information, contact us today!