Whether recovering a valuable component from waste, drying a precursor material, or performing a chemical reaction to yield an end product, establishing a safe, effective, and efficient thermal process often relies on thermal testing procedures like those carried out in the FEECO Innovation Center.
Testing gives producers the opportunity to develop product characteristics, refine process variables, troubleshoot issues, and turn their ideas into sophisticated process solutions ready for commercial-scale production.
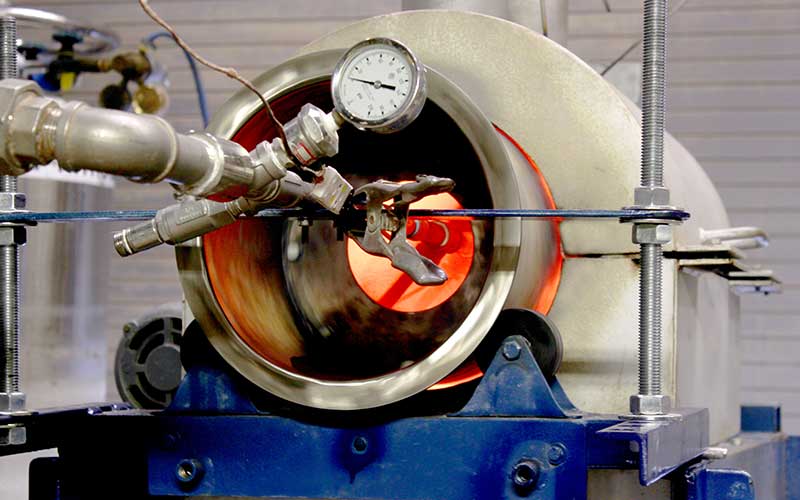
Batch Indirect Rotary Kiln used for testing in the Innovation Center
What Is Thermal Testing?
Thermal testing is applicable to a broad scope of processes. In this setting, we’re referring to the testing of various industrial processes that use temperature to cause a physical change or chemical reaction in bulk solids.
The Innovation Center works specifically with industries like mining and minerals, chemicals, forest products, and more, to help processors establish new processes, troubleshoot existing ones, and develop the data required for commercial-scale production of the intended process.
Examples of thermal processing tests conducted include:
- Drying (Rotary or Fluid Bed)
- Calcination
- Waste Incineration
- Metal Recovery
- Catalyst preparation and production
- Biochar production
- Activated Carbon production
- Upgrading of ores (ex., phosphate rock)
- Reduction roasting
This diversity of potential applications requires a flexible approach to testing. For this reason, the Innovation Center is equipped with a range of thermal testing units, at both batch and pilot scale.
Red mud samples taken throughout testing in a reduction roasting process.
Why Consider Thermal Testing?
Testing is useful at every stage of the process lifecycle, from assessing initial feasibility, to developing and maintaining a safe and efficient thermal process.
Developing New Processes
In developing a new process, testing is used to:
- Reduce investment risk
- Maximize process efficiency
- Reveal unexpected issues early in the design stages as opposed to after commissioning when resolution is much more costly.
- Establish the most efficient equipment configuration
- Develop process criteria such as flow rates, percent fill, temperature profiles, and more.
FEECO can successfully take customers from the beginning design stage, to the final process and equipment solution, assisting the customer in:
Step 1: Planning the Testing Process
Customers work with a process sales engineer to summarize project goals and specifics. A report is then created to outline the preliminary budget proposal and solution details.
Step 2: Testing
Once the test plan has been finalized, FEECO’s experienced personnel perform the tests needed to achieve testing objectives. Depending on the process and what is already known, this might include feasibility studies, evaluating different production conditions, establishing the parameters required for continuous operation on a commercial scale, and more. A benefit analysis is derived from the test results.
Step 3: Conceptual Engineering
The conceptual engineering step may include finalizing equipment selections, drafting a Process Functional Description, creating electronic drawings of equipment designs and layouts, and planning preliminary risk prevention and mitigation.
Step 4: Plant Design & Construction
Once the steps above have been completed, FEECO can move forward with customers to successfully implement finalized process designs and equipment manufacturing.
“Testing in the Innovation Center is a risk management tool that reduces process complications for customers. We can work out process bugs and study the effects of unknown variables before customers spend a large amount of capital on their process and related equipment. In addition to lowering process-related risks, customers also benefit from a higher probability for success compared to processes implemented without the support of testing,” says Alex Ebben, FEECO Process Sales Engineer and thermal processing expert.
Thermocouples measure air and material temperatures inside a direct-fired batch kiln
Optimizing Existing Processes
FEECO can model a customer’s system at batch and pilot scale and analyze the thermal process in question. Variables are evaluated in a controlled environment in order to characterize the effects of changes on the process.
Customers struggling with operational problems find that testing in a dedicated facility is a much more cost-effective and convenient way to identify and resolve problems versus running trial-and-error processes in their own facility.
Thermal Process Testing Equipment
The Innovation Center includes batch equipment, a pilot plant, and an analytical laboratory. Whether a material requires testing in a stand-alone thermal processing unit, or in a continuous process loop, the FEECO Innovation Center is equipped to meet the bulk solids drying and high-temperature thermal processing needs of diverse applications.
Our test units have the ability to accommodate a variety of high-temperature applications such as calcining mined minerals and separating precious metals from unwanted elements. The facility also offers the ability to monitor various discharges from thermal processes. Available thermal processing test equipment includes:
Rotary Dryer | Rotary Dryer with Recycle Loop
The test rotary dryer is often used in establishing pre-treatment drying requirements, as well as process and material requirements for standalone drying operations, and those needed for producing a granular product to specification.
Potash in the Innovation Center’s pilot dryer
Fluid Bed Dryer | Fluid Bed Dryer with Recycle Loop
As with the test rotary dryer, the test fluid bed dryer is used in pre-treatment drying applications, as well as developing process and material requirements for standalone drying operations, and those needed for producing a granular product to specification.
Test Fluid Bed Dryer
Direct-Fired Rotary Kiln – Batch and Continuous
A direct-fired rotary kiln exposes material to direct contact with a heat source when traveling through the kiln’s interior. This type of kiln is considered to be a very robust and efficient heat transfer unit. Associated gas handling equipment is also available for testing with this unit. FEECO can accommodate both batch- and pilot-scale testing in a direct-fired rotary kiln.
Indirect-Fired Rotary Kiln – Batch and Continuous
An indirect kiln transfers heat through the shell, avoiding direct contact between the material and process gasses. This type of kiln offers a controlled environment and enhanced process controls. Associated gas handling equipment is also available for testing with this unit. Again, both batch- and pilot-scale testing are possible.
Rotary Drum Flight (Lifter) Test Unit
The FEECO rotary drum lifter test unit can simulate flight design and arrangements within rotary equipment, enabling customers to optimize flight designs before finalizing their equipment design. A clear-capped end allows for visual observation of flight performance.
This unit can also be equipped for testing bed disturbers and tumbling flights in order to evaluate material bed rotation and agitation options.
Different flight designs, indicated by yellow and blue tape, are tested in the flight simulator
Beyond Thermal Testing: Support Equipment & Analysis
In addition to extensive thermal testing capabilities, the Innovation Center is also equipped with a variety of equipment and procedures to evaluate process conditions throughout the testing process. This includes the ability to:
- Analyze exhaust gasses
- Evaluate dust levels and potential for attrition
- Establish volumetric flows
- Meausure gas concentrations
- Identify thermal losses
- Reveal inefficiencies
A range of material characteristics can also be tested, including:
- Green strength of pellets
- Dry pellet crush strength
- Particle size distribution
- Angle of repose
- Moisture analysis
- Loss on ignition
- Product flow characteristics
This is in addition to the Innovation Center’s ability to incorporate thermal testing as part of a larger agglomeration/granulation, coating, or mixing process. An extensive line of ancillary equipment is also available to support processes, including belt conveyors, a bucket elevator, a steep incline conveyor, muffle furnace, steam generator, batch walk-in oven, fluid bed sample dryer, and spargers.
What You Can Expect From Thermal Testing
Since 1951, we have worked to cultivate a testing environment that joins process design with material knowledge throughout the entire testing experience. Staffed by experts and outfitted for a range of testing possibilities, the FEECO Innovation Center is capable of analyzing a wide range of thermal processes from start to finish. This means you get the answers you need at every step of the way.
To learn more about our thermal processing test and equipment capabilities, contact us today!