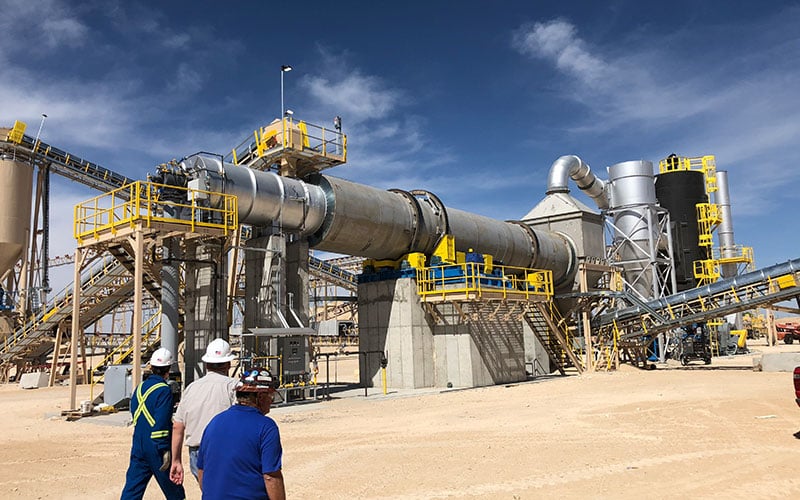
Rotary Dryer Service Inspection
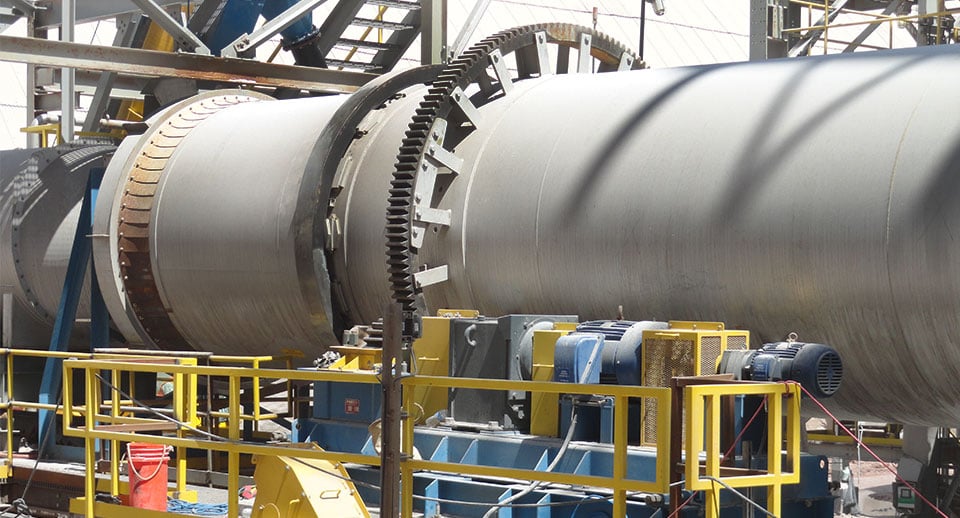
Rotary Dryer Repair
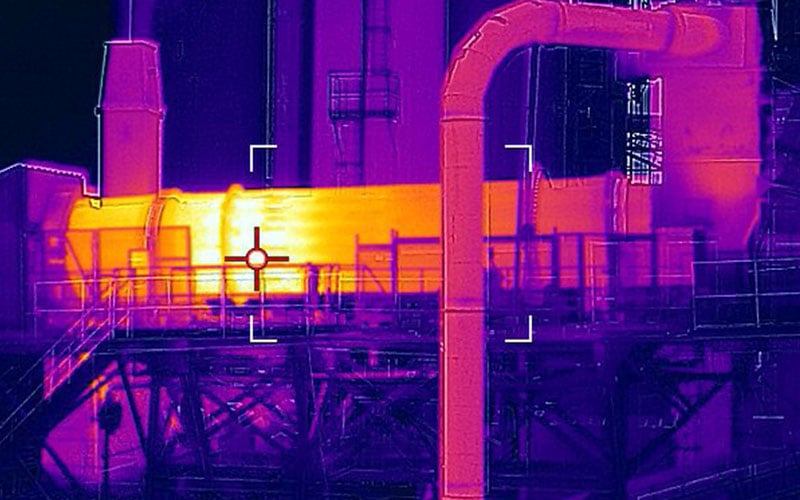
Rotary Kiln Thermal Imaging
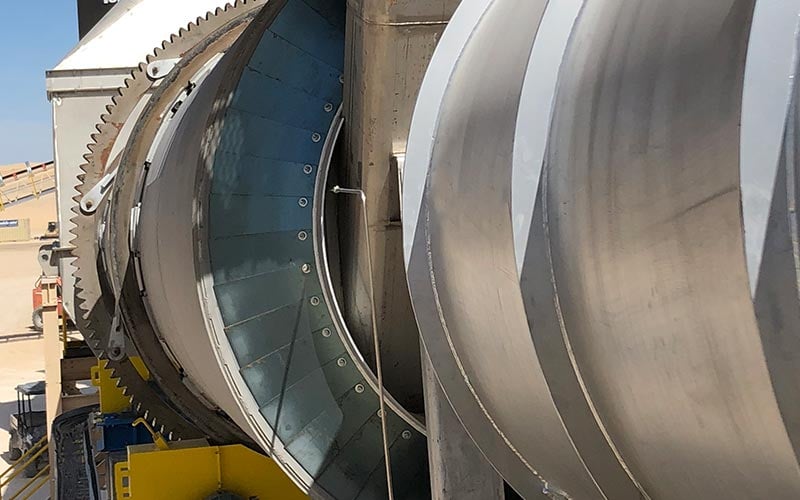
Leaf Seal on a Rotary Dryer
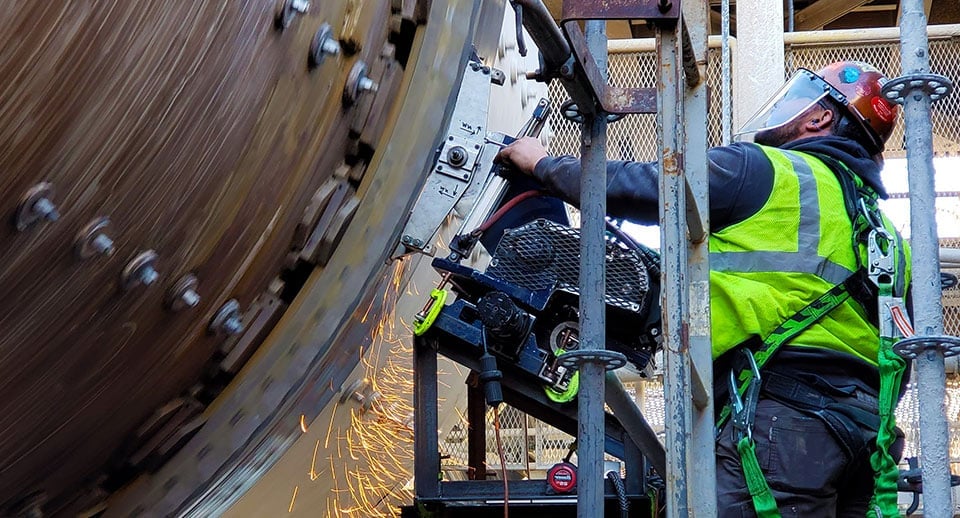
Rotary Kiln Maintenance
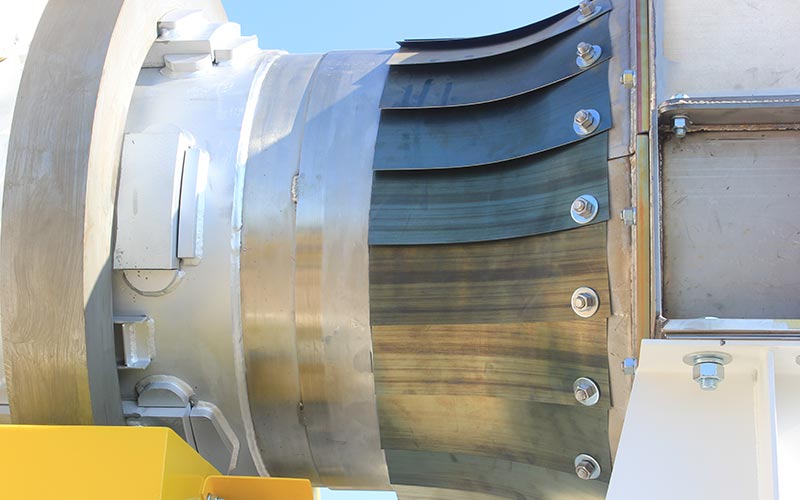
Leaf Seal on a Rotary Kiln
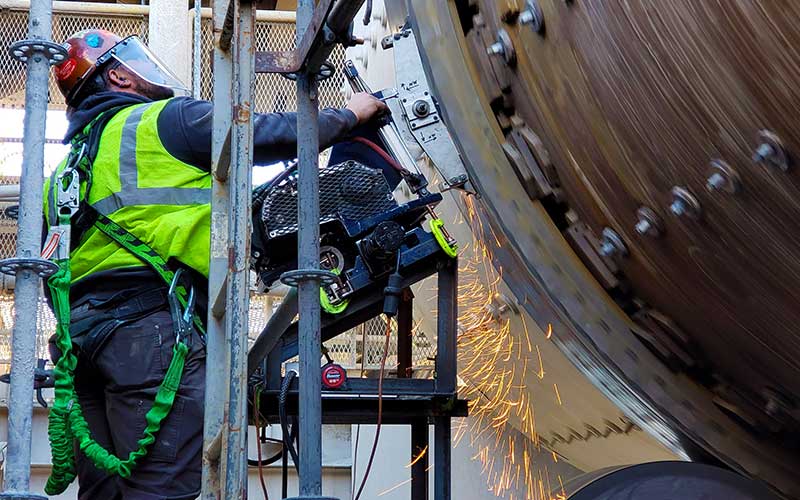
Tire Grinding in Progress
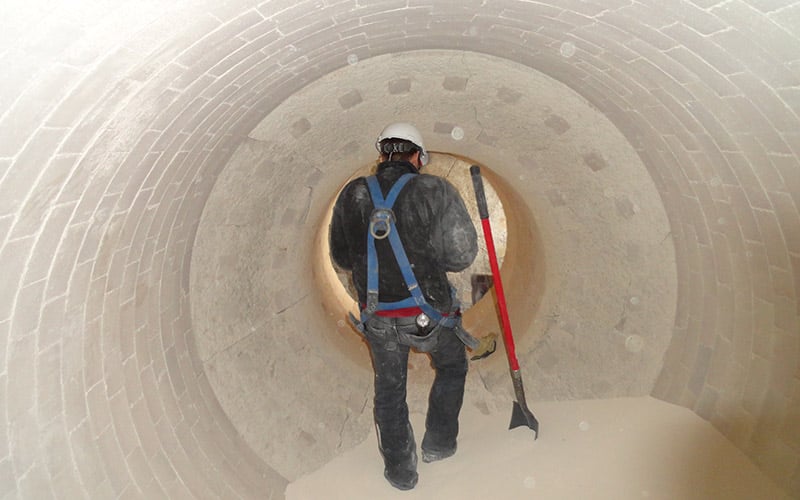
Rotary Kiln Inspection in Progress
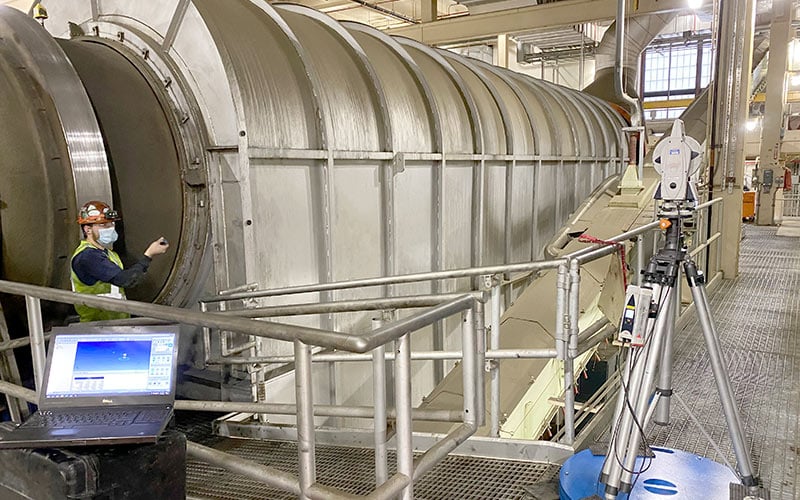
Rotary Dryer Realignment in Progress
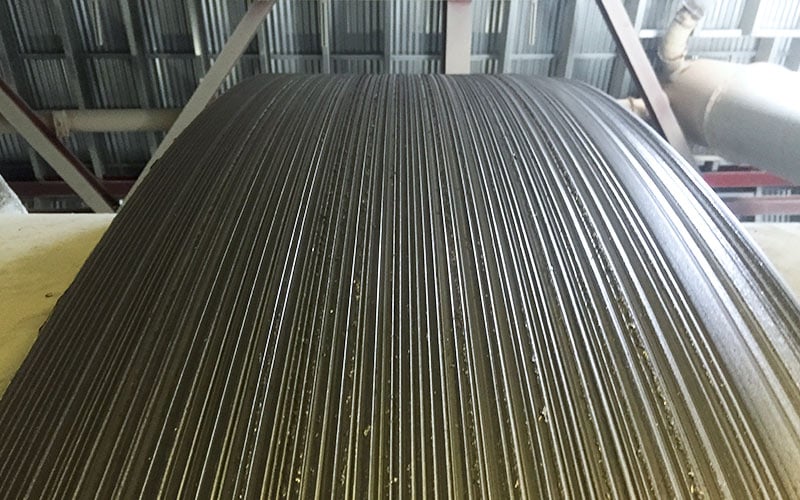
Worn Tire on a Misaligned Rotary Dryer
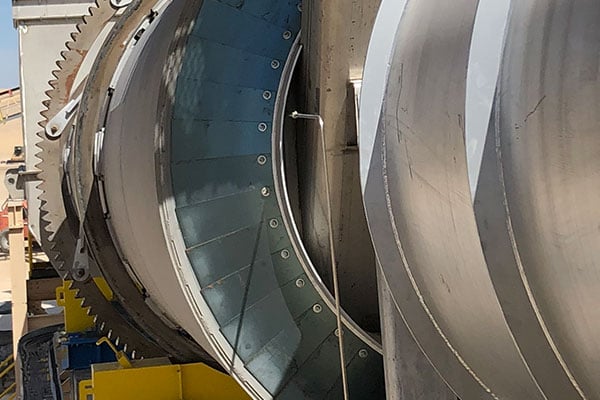
Rotary Drum Leaf Seal
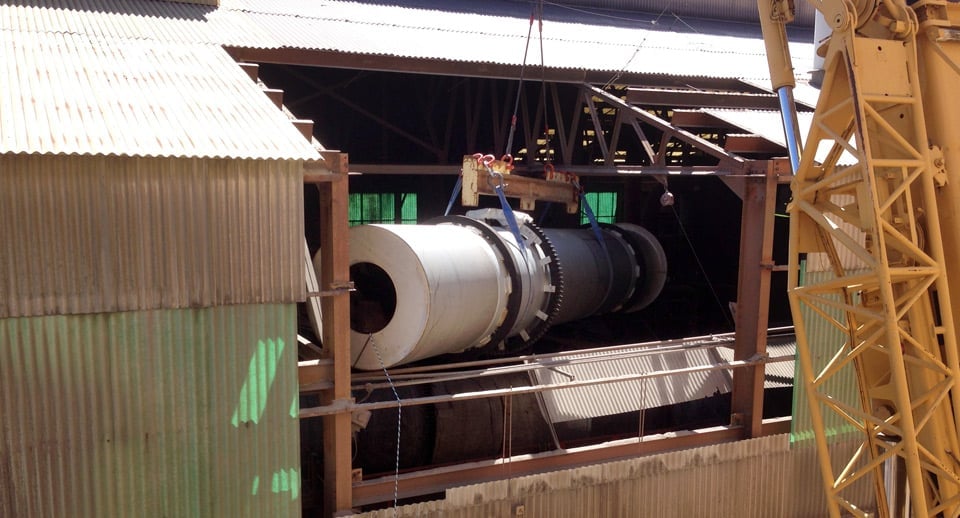
Replacement Equipment and Spare Parts
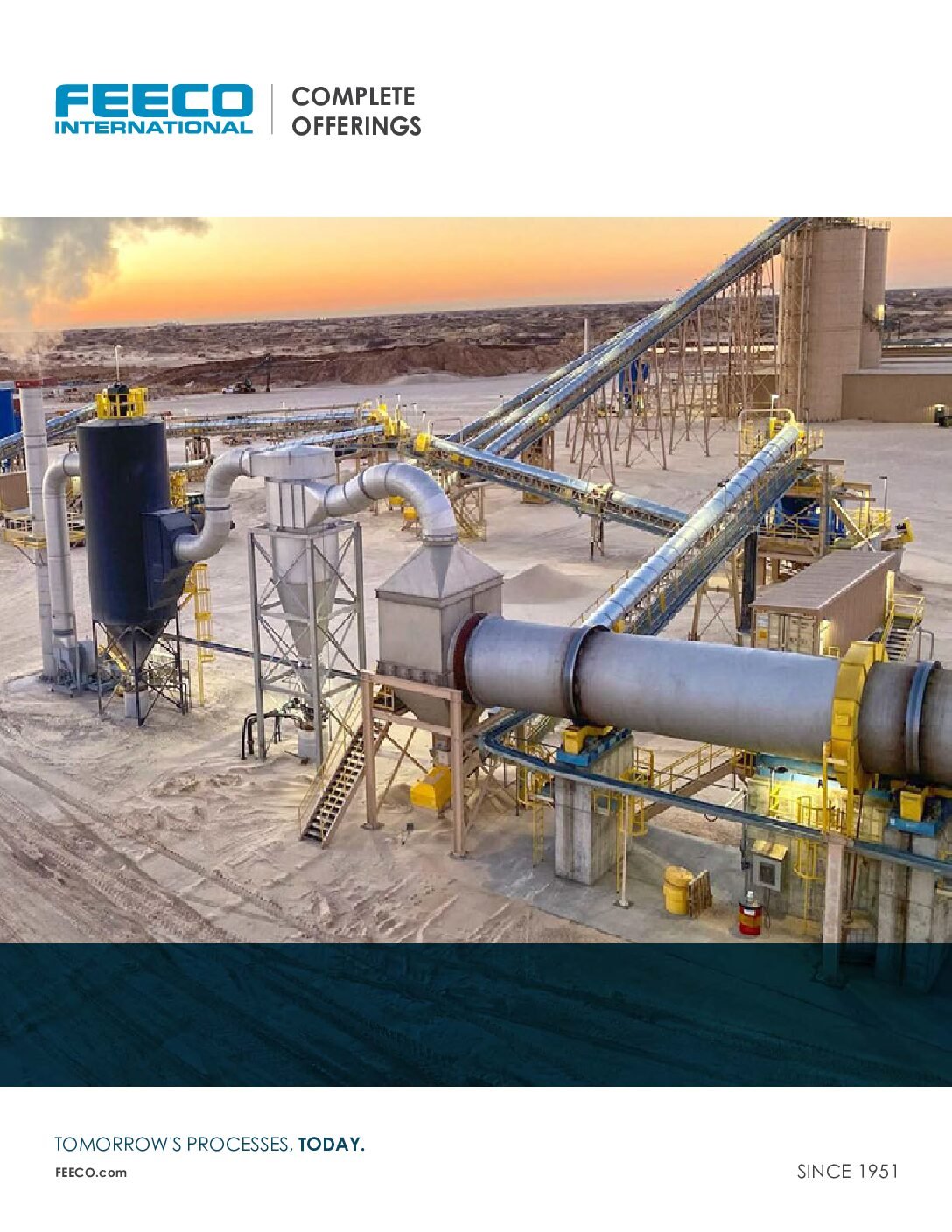
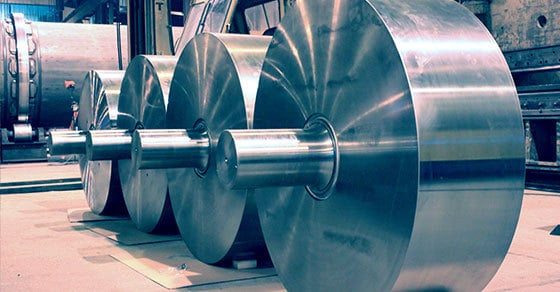
Trunnion Wheels
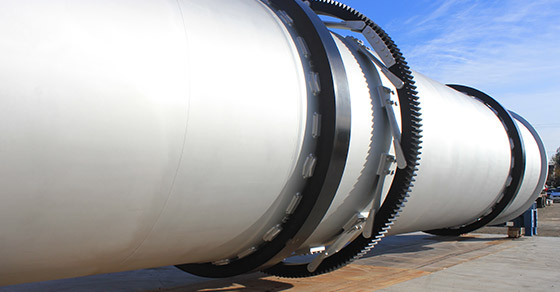
Girth Gear
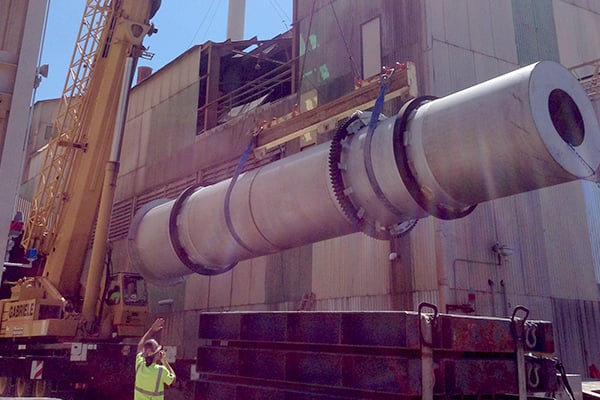
Rotary Drum Replacement in Progress
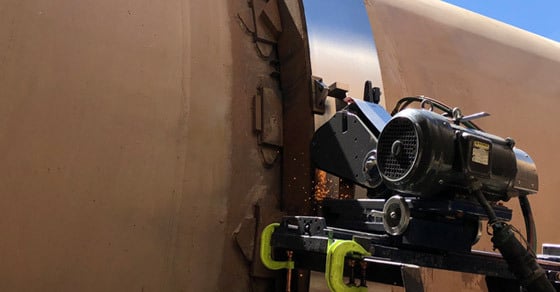
Tire Grinding
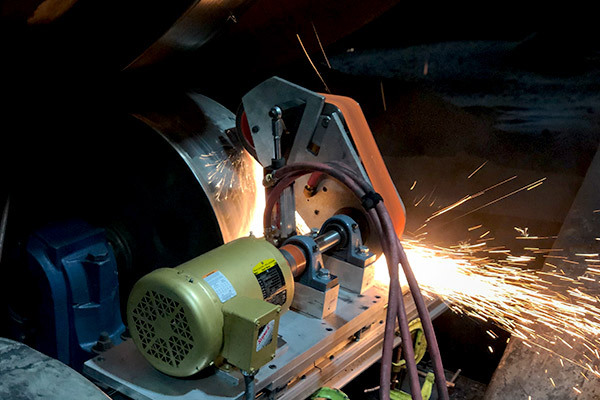
Trunnion Grinding in Progress
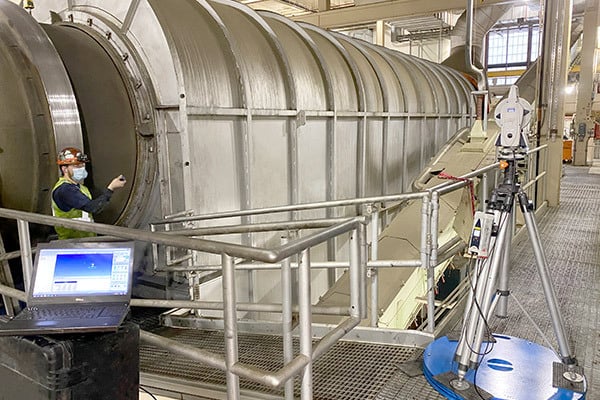
Rotary Drum Shaft Laser Alignment
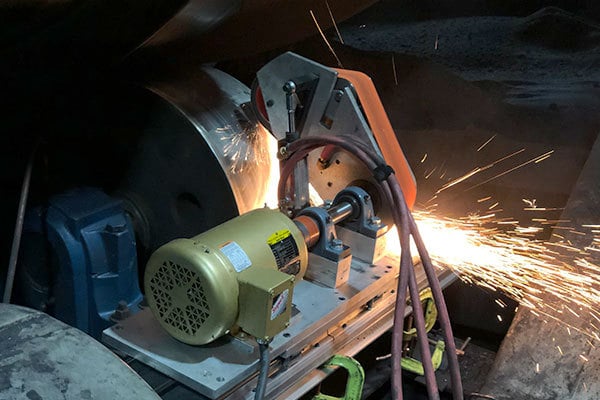
Trunnion Wheel Grinding

Replacement Trunnion Wheels
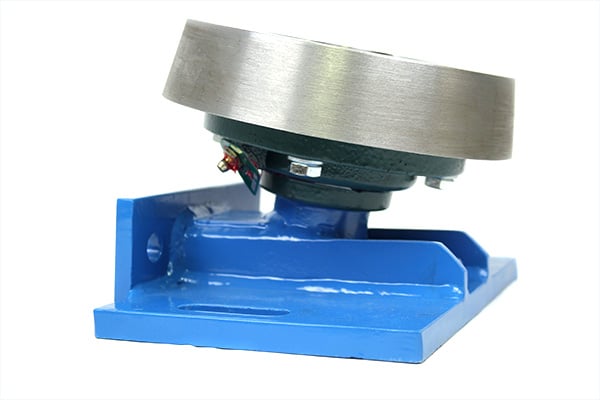
Thrust Roller Assembly
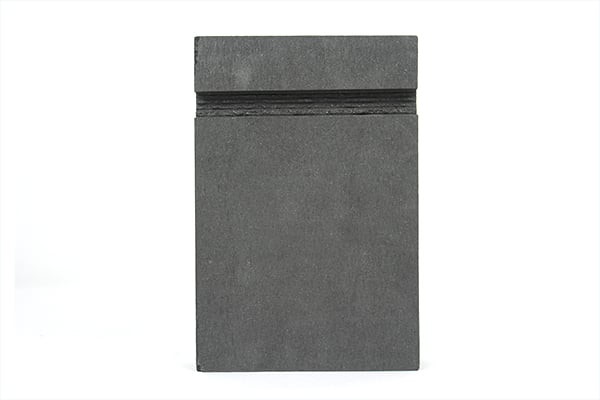
Graphite Lubrication Block

Rotary Drum Spare Parts
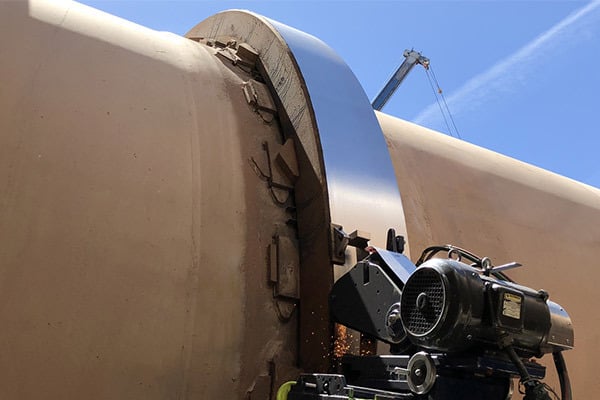
Tire and Trunnion Grinding
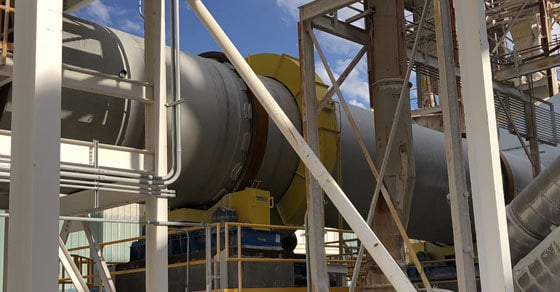
COVID-19 Demands Aftermarket Services

Pyrolysis Kiln Seal
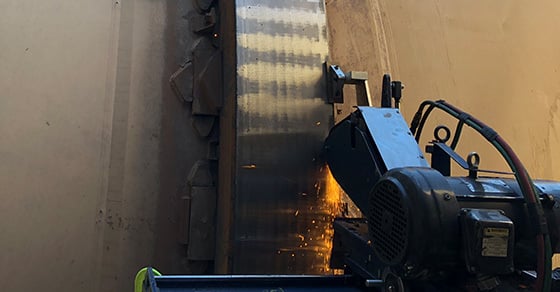
Tire Grinding FAQ
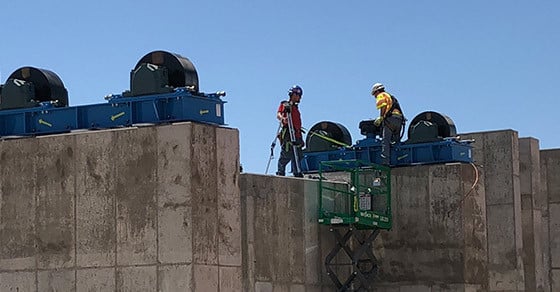
FEECO Remote Services During COVID-19
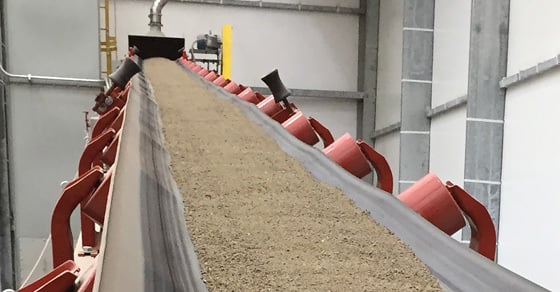
Troubleshooting Belt Conveyors
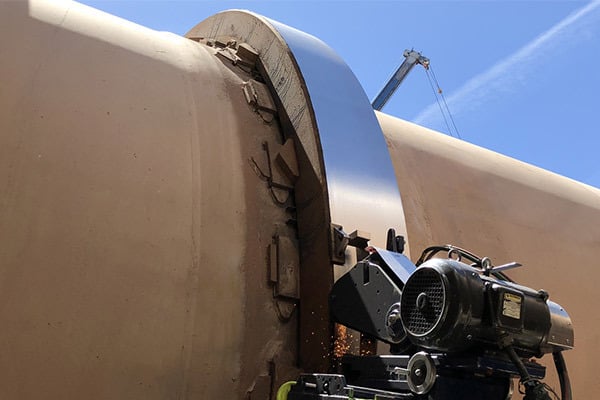
Tire and Trunnion Grinding
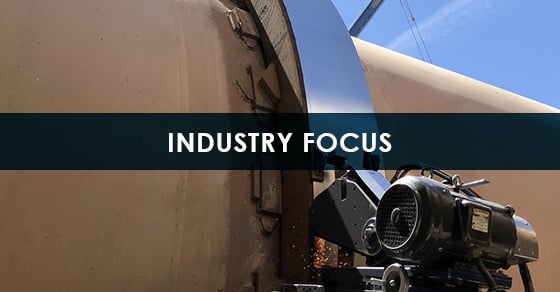
Rotary Kiln Incinerator Maintenance
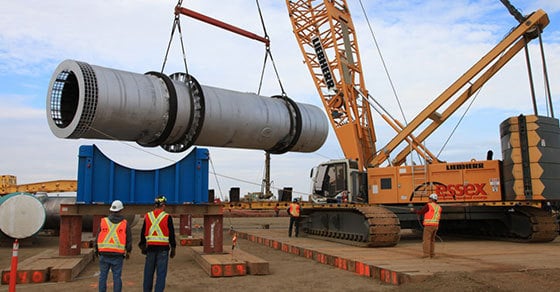
Rotary Drum Dryer (Drier) Replacement
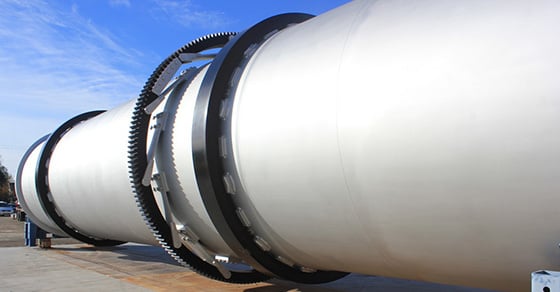
Rotary Drum Shell Issues
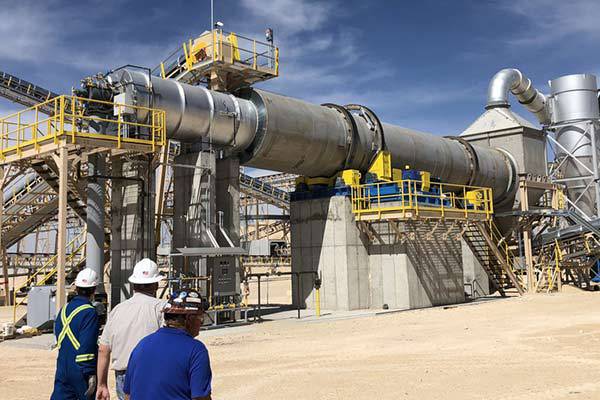
Rotary Drum Inspection
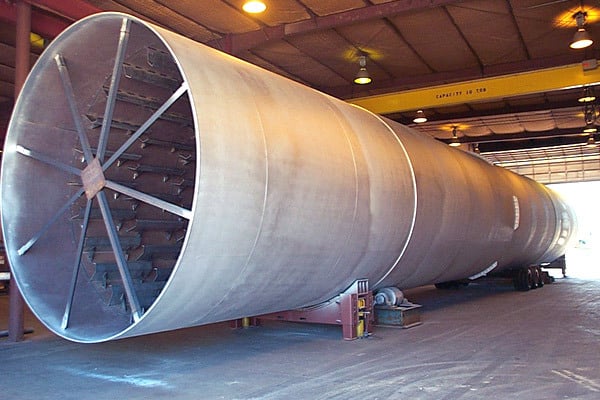
Replacement Rotary Drum Shell
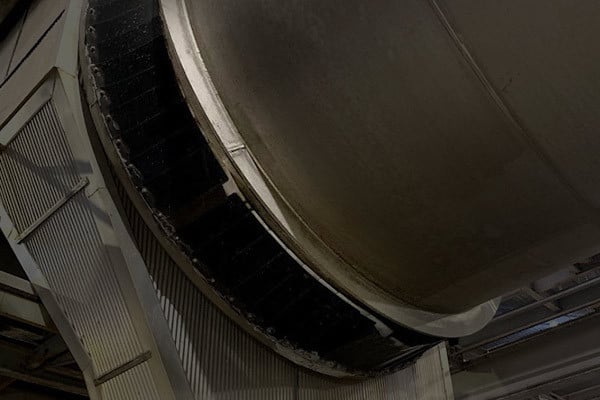
Rotary Drum Stiffening Ring
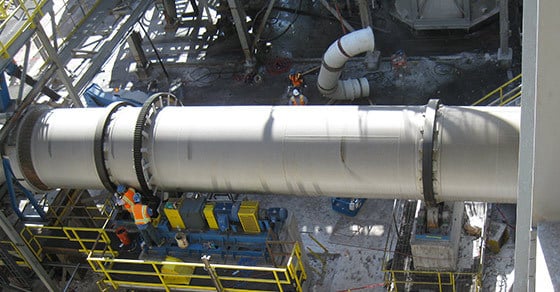
Surviving the Manufacturing Slowdown with Proactive Rotary Drum Maintenance
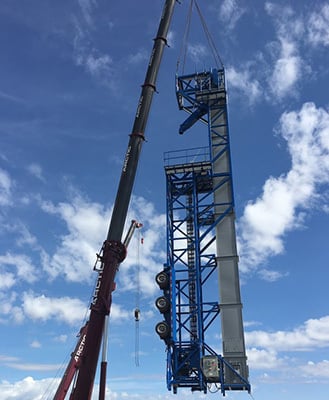
Bucket Elevator Replacement
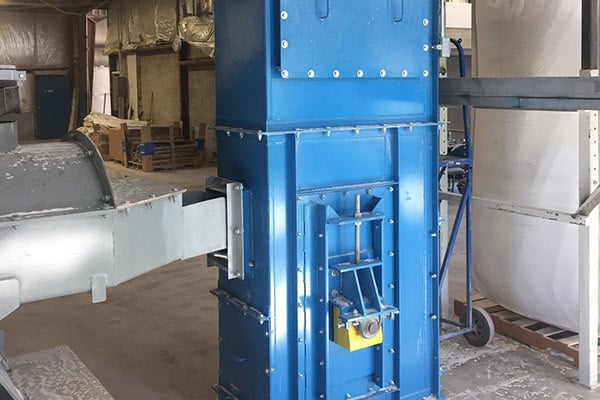
Bucket Elevator Replacement Boot Section

Bucket Elevator Replacement

Knowing When its Time to Replace Your Rotary Drum Seal, Leaf Seal

Boomin Catalyst Market Drives Demand for Rotary Kiln Maintenance

Replacement Dryer (Drier) and Kiln Burners

Improving Feedstock Uniformity to Optimize Bulk Solids Processing
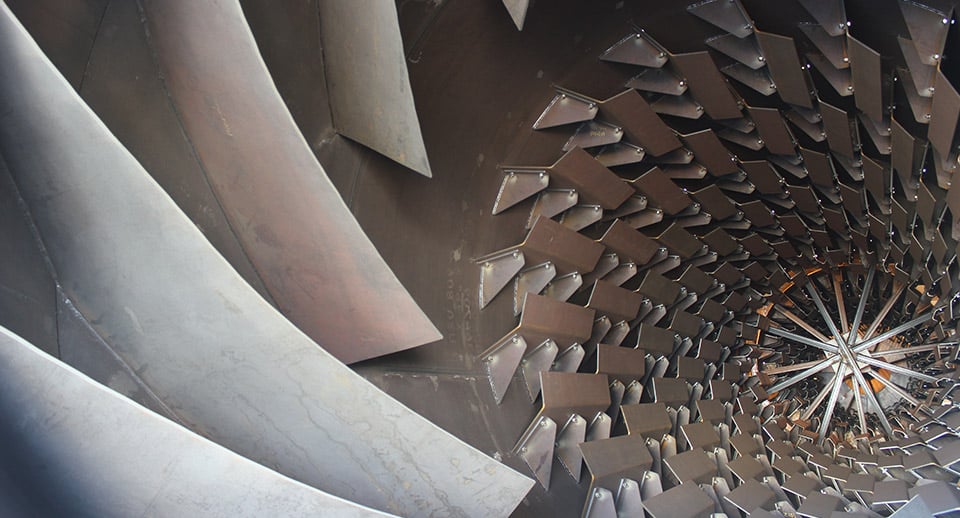
Replacement Drum Flights, Rotary Dryer (Drier) and Cooler Flights
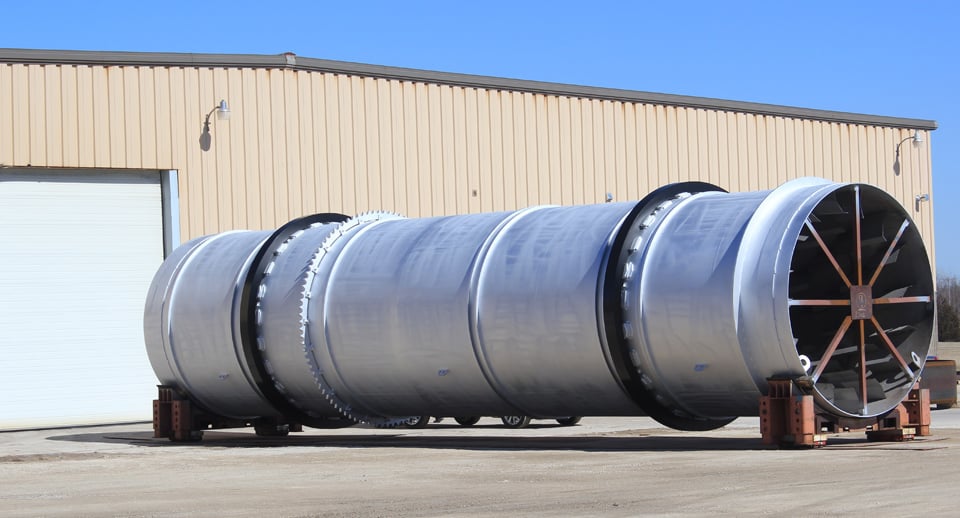
Replacement Rotary Drum Shell
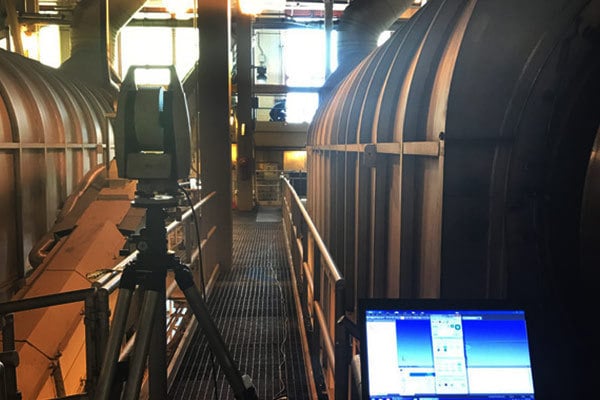
Rotary Drum Laser Alignment Process, Rotary Drum Alignment
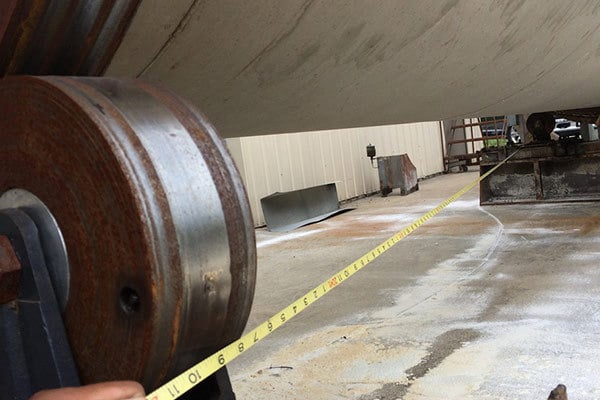
Rotary Drum Alignment, Misalignment

Why Post Maintenance Rotary Drum Alignment is Critical
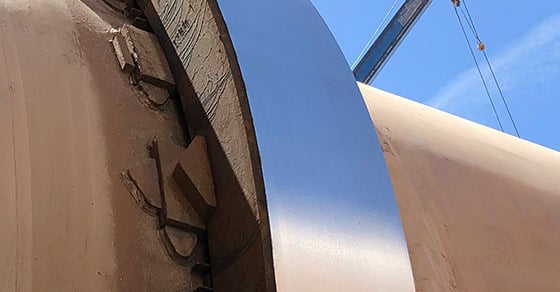
Causes of Tire (Tyre) and Trunnion Wear, Rotary Drum Tire
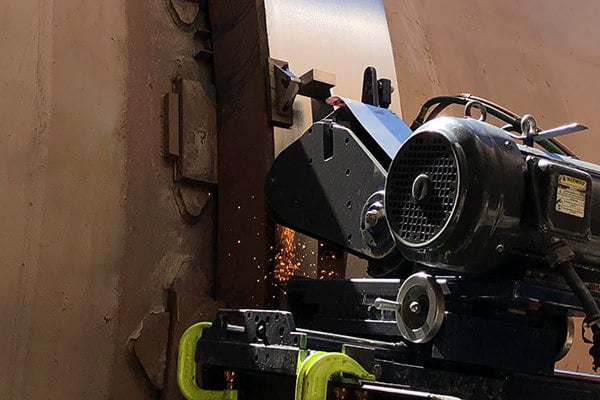
FEECO Tire (Tyre) Grinding Machine, Tire and Trunnion Grinding in Progress
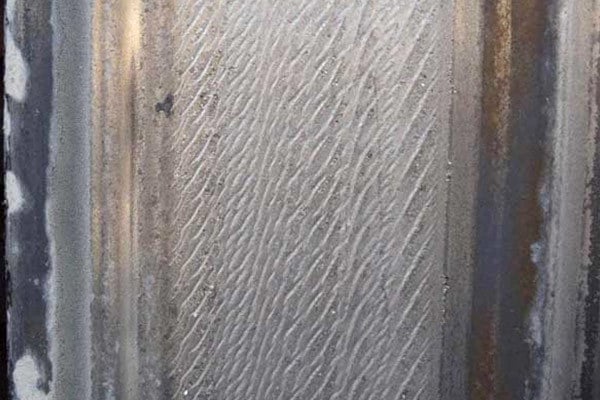
Rotary Drum Tire (Tyre) Wear Pattern from Excessive Wheel Skewing, Rotary Drum Tire in Need of Tire Grinding

Rotary Drum Tire (Tyre) Wear Pattern from Poor Housekeeping Practices, Rotary Drum Tire in Need of Tire Grinding

Rotary Drum Tire (Tyre) Wear Pattern from Misalignment, Rotary Drum Tire in Need of Tire Grinding
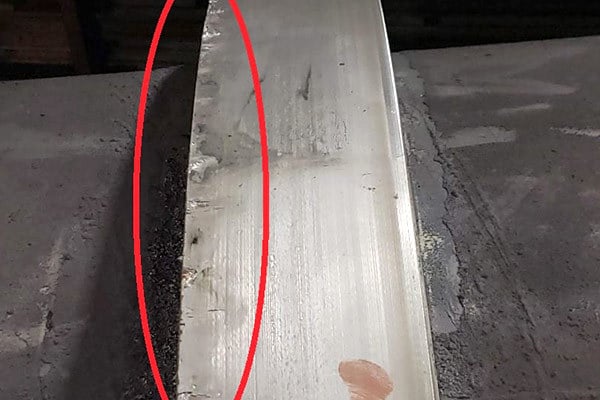
Rotary Drum Tire (Tyre) Wear Pattern from Using Improper Tire Lubricant, Rotary Drum Tire in Need of Tire Grinding
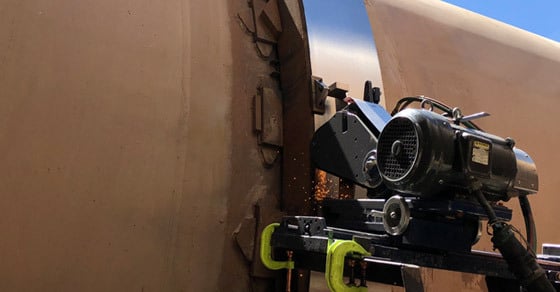
Tire (Tyre) and Trunnion Wheel Grinding
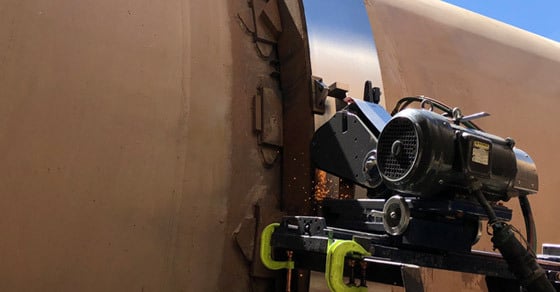
Tire (Tyre) and Trunnion Grinding
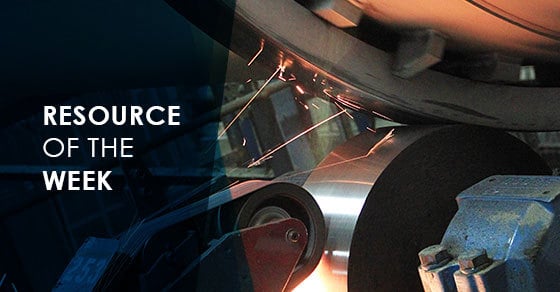
Resource of the Week: Tire (Tyre) Grinding Page
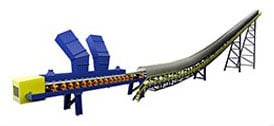
Replacement Conveyor Parts
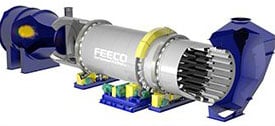
Replacement Rotary Drum Parts
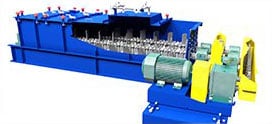
Pugmill Mixer (Pug Mill, Paddle Mixer) Replacement Parts
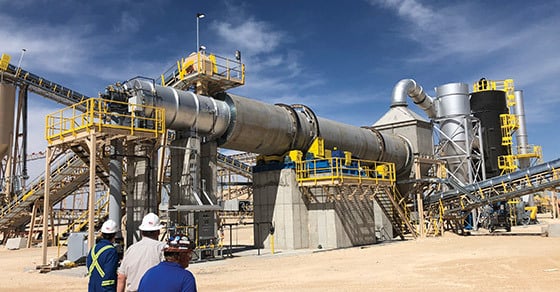
Rotary Dryer (Drier) Process Audits

Rotary Kiln System Optimization, Rotary Kiln Process Audit
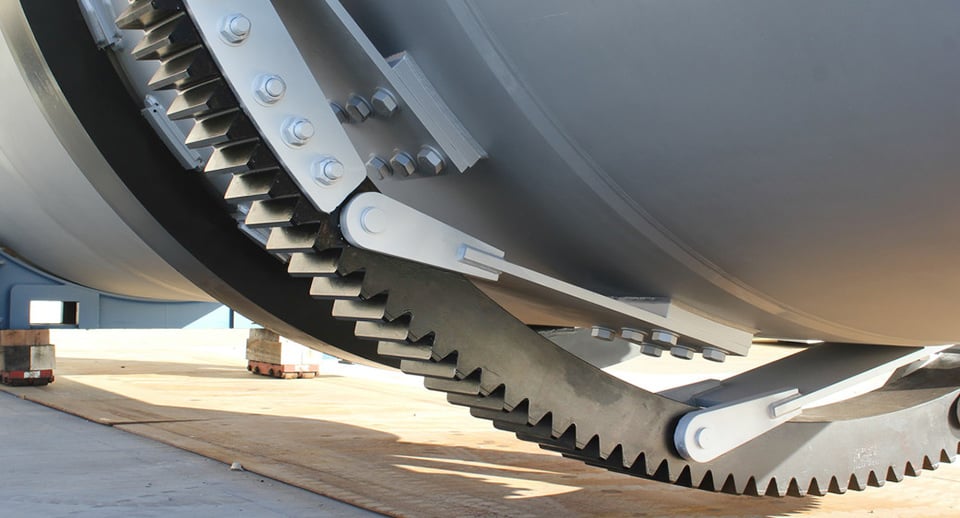
Spring-Mounted Replacement Rotary Drum Girth Gear
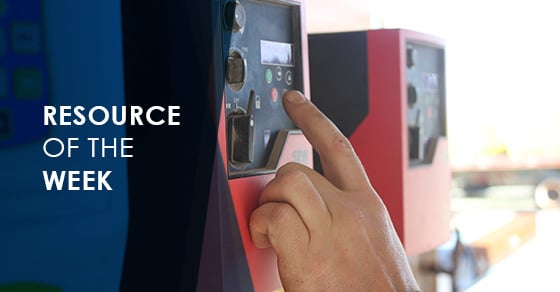
Resource of the Week: Aftermarket Brochure
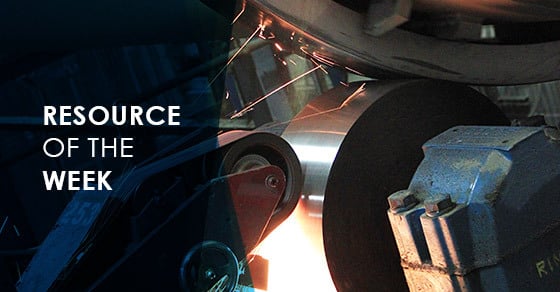
Resource of the Week: Tire (Tyre) Grinding Page

Rotary Kiln Refractory Failure Illustration, Rotary Kiln Shell Hot Spot
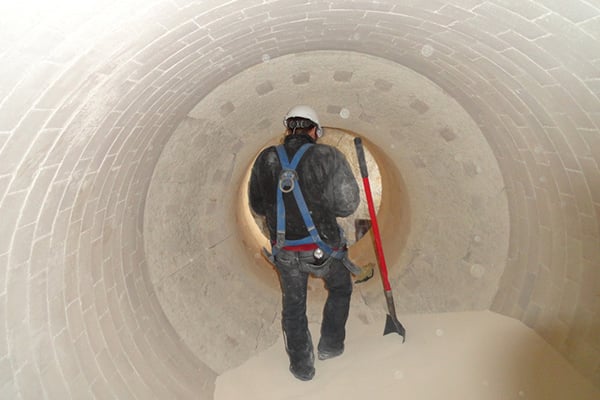
Rotary Kiln Refractory Inspection
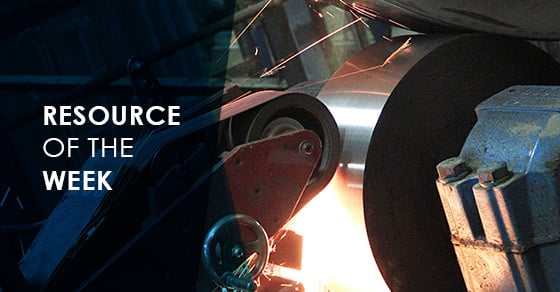
Resource of the Week: Tire Grinding Brochure
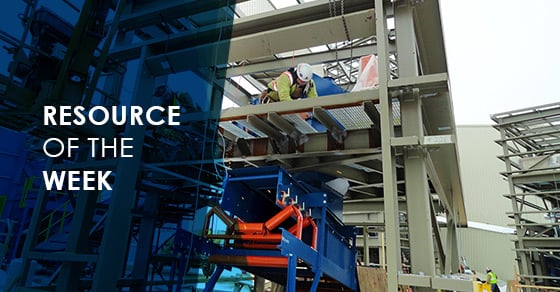
Resource of the Week: Services Page

Seal options for rotary dryers (driers), coolers, kilns, drums

Rotary Drum Seal
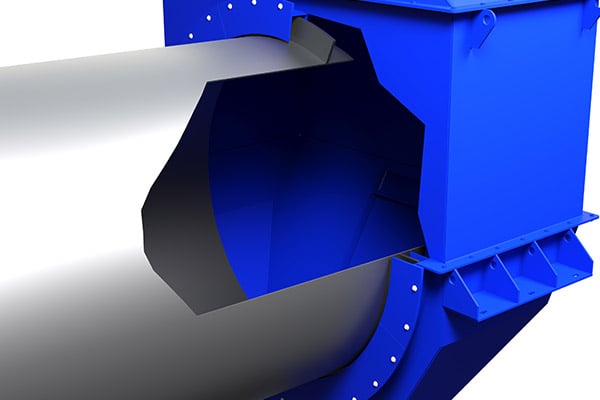
3D Model of a Labyrinth Seal for Rotary Drums
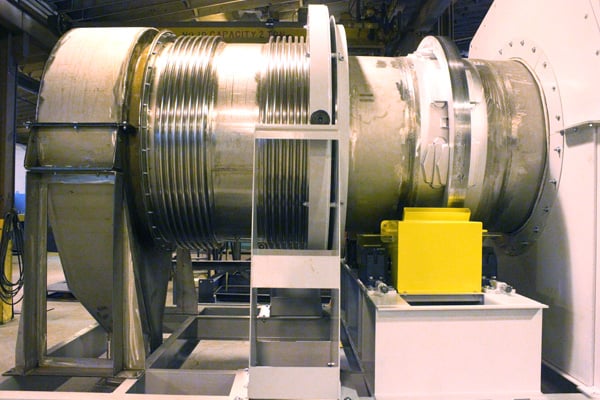
Rotary Drum Bellows Seal