Rotary coolers offer an effective approach to cooling bulk solids exiting a rotary kiln or dryer, allowing material to safely move on to packaging, handling, or transport.
These diverse industrial coolers are available in two primary configurations: convective (direct) and indirect water deluge, each with their own advantages. What follows is an overview on each type.
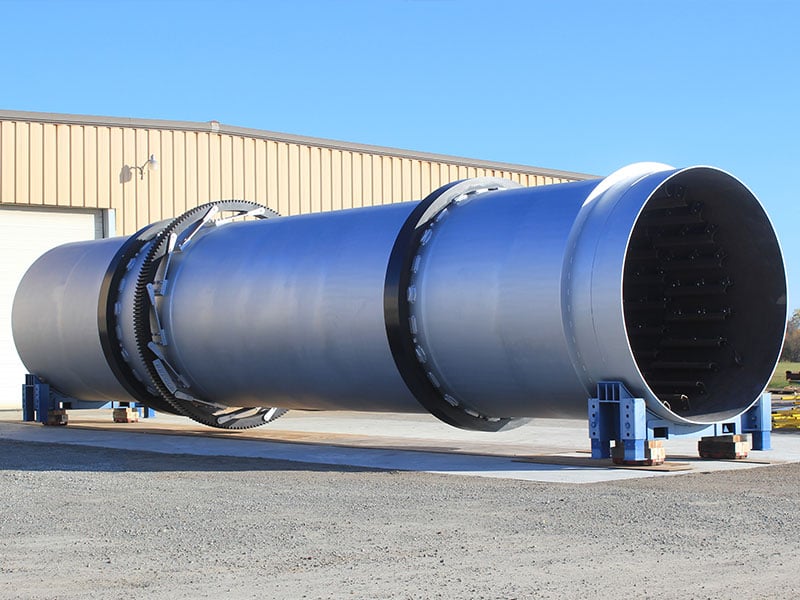
FEECO Rotary Cooler ready for shipment
Why Rotary Coolers?
While a number of process cooling equipment technologies exist, the rotary cooler type has become the preferred approach for many manufacturers working with bulk solids.
Rotary coolers can cool bulk solids at a throughput in excess of 200 TPH, making them the choice for high-capacity settings such as those found in the fertilizer industry. They are also extremely reliable, simple to operate, and have a high tolerance for variation in feedstock. Rotary coolers can accommodate temperatures anywhere from 150°F to over 1000°F, making them ideal for use after a rotary kiln or dryer.
They also provide significant opportunity for customization, with numerous add-ons and modifications possible for a solution truly tailored to meeting product and process goals.
Convective (DIRECT) Rotary Coolers
A convective rotary cooler works like a rotary dryer without heat; material and the cooling medium, typically ambient or chilled air, are passed through a rotating drum set on a slight angle.
The material and cooling medium are in direct contact and lifting flights pick up and shower the material through the chilled air in a cascading motion while the drum rotates.
Convective rotary coolers are always of the counter-current design, meaning the material and air stream flow in opposing directions. In other words, the material is fed into one end of the drum while the chilled air is fed into the other and the two move through the drum in opposing directions, taking advantage of the increased heat transfer and improved thermodynamics characteristic of this design.
In some convective rotary coolers, it is necessary to line the inlet of the rotary drum with refractory, because some material temperatures may exceed the design temperature of the rotary drum shell, typically carbon steel. The refractory is installed in the front end of the rotary cooler until the material has reached a temperature that the shell can handle. At this point, the refractory stops, and internal lifting flights begin to shower the material.
Interior view of rotary cooler with flights
Indirect Rotary Coolers
In contrast, indirect rotary coolers, also known as water deluge or water-jacketed coolers, are employed in production settings where the material either cannot come into contact with an airstream, or would otherwise become entrained in one. Instead, material moves through the rotating drum while cool water bathes the drum’s exterior, thereby cooling the material sliding against the shell’s interior.
A trough above the rotating drum bathes the rotary drum in cool water, which is then collected at the bottom and sent through a heat exchanger for re-cooling. The water can then be recirculated to the trough above the drum.
Due to the constant exposure to water, a carbon steel shell would be inappropriate in this setting. Instead, an indirect water deluge rotary cooler is constructed of stainless steel to avoid corrosion. If the material entering the drum is expected to exceed a certain temperature, the inlet portion of the drum may utilize a specialty alloy to prevent heat damage.
The use of refractory would be impractical in the case of an indirect cooler, as it would create an additional heat transfer barrier, reducing efficiency.
3D Rendering of an indirect water deluge cooler
Direct or Indirect?
The direct cooler is most efficient for the majority of industrial process cooling needs, but there are two key settings in which the indirect cooler provides a valuable alternative:
When Atmospheric Control is a Priority
When material must be kept in an inert atmosphere, such as when processing certain types of chemicals, the use of an indirect cooler allows the processor to maintain the required atmosphere inside the unit. For this reason, indirect coolers are widely used in processing recovered EAF dust in the form of pellets.
When Processing an Ultra-Fine Material
When processing ultra-fine materials such as technical ceramics, an indirect cooler is often chosen to avoid the material becoming entrained or picked up in the velocity of the air stream and carried out with the exhaust gas.
Conclusion
Rotary coolers are ideal for processors looking for a high-capacity, reliable process cooling solution they can tailor to their specific requirements. The most suitable configuration depends on the material characteristics, as well as process and product goals.
FEECO has been manufacturing and servicing the industry’s most reputable rotary coolers since 1951. For more information, contact us today!